HVAF: High Velocity Air Fuel
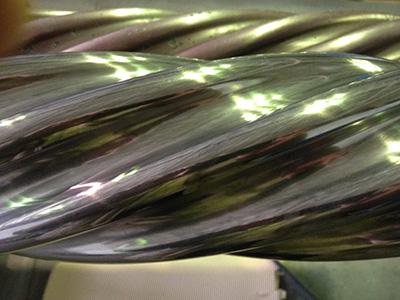
HVAF coatings are similar to and are generally comparable to coatings produced by HVOF and Cold Spray. HVAF is a "warm spray" process that is cooler than HVOF, but hotter than Cold Spray. HVAF guns utilize axial powder injection into an air-fuel jet with a temperature of about 1900-1950°C. Therefore, the process is capable of effectively applying carbide-based materials, but since the air-fuel jet produces considerably less oxides than high temperature oxy-fuel jets, the HVAF process can also apply metals with almost zero oxidation, similar to Cold Spray. All common thermal spray powder materials may be applied with HVAF, except for ceramics.
High Velocity Air Fuel:
- a derivative of conventional HVOF
- uses compressed air instead of oxygen
- higher spray rates and deposit efficiency
- faster spraying and lower application cost
- harder, better performing coatings due to the "warm spray" nature of the process
- surface preparation is done with the spray gun
Features | Benefits |
Drop in replacement for HVOF | Easy to implement with existing spray booth and hardware. |
Better quality coatings: higher density, better wear resistance, better bond strength | Coatings perform better in service. |
Faster spray rate | Complete jobs in less time with less cost. |
Higher deposit efficiency | Use less powder to make coatings. |
Much lower spare parts consumption | Gun does not wear quickly, maintenance costs are vastly reduced. |
Robust materials of construction | Gun is not easily damaged by operator mistakes. |
Easily configurable to spray a broad range of materials and achieve various coating properties | An HVAF gun can spray practically any metal or cer-met by simply changing the hardware configuration. |
No need to maintain oxygen storage | Less real estate is required to set up an HVAF system. |
No chilled water requirement | Gun is easier to maintain, there is no mess when it is taken apart. |
Portable | Can be used in workshop or on-site. |
Fully automatic | Controller monitors inlet and outlet conditions to maintain set points. |
Built in data logging | Provides detailed record of spray history for documentation. |
Unlimited recipe storage | Store custom parameter sets with descriptive text for each coating material or part. |
Autospray function completely automates spray process | Saves time and labor, anyone can spray good coatings. |
Grit blast with the gun | Operators set parts one time, grit blasting and coating occur in one location. Greatly reduces preparation time and cost. |
Remote diagnostics | Factory assistance available at no charge, no need to wait for service technician to travel to customer site. |