The M3™ supersonic HVAF spray gun delivers the highest quality cemented carbide coatings. The M3™ can apply all HVOF powders (-45+15 μm), as well as special HVAF cuts (-30+5 μm, -30+10 μm). Metals and metal alloys can also be effectively applied.
The M3™ produces not only high particle velocity, but also high particle temperature, compared to single-nozzle HVAF spray guns. This allows the M3™ to produce impermeable tungsten carbide coatings with hardness of up to 1670 HV300 and negligible W2C content. Standard HVOF cut powders (-45+15 μm) can also be sprayed with hardness of 1350 HV300.
Tungsten carbide and chrome carbide coatings sprayed with M3™ have passed high pressure gas permeability tests at 15,000 PSI, with 100% success rate.
M3™ coatings meet or exceed the coating requirements of Aerospace Material Specification (AMS 2447 Rev. D).
Powder | Cut | Velocity | D.E. | Spray Rate |
WC-based powders | -45+15 μm -30+5 μm -25+5 μm | 960 - 1250 m/s | 46-62% | 34 kg/h max |
CrC-based powders | -25+5 μm | ~ 1300 m/s | 40-55% | 18 kg/h max |
- WC-based coatings with hardness of up to 1670 HV300
- Coating porosity typically below 0.2%
- Compressive residual stresses in coatings
- Negligible oxide content in coatings (1.5-2 times that of feed stock material)
The M3™ spray gun operates on Propylene or Propane. Highly efficient 100% air cooling eliminates the need for a chilled water supply.
The cost of coating application with M3™ is 2-4 times lower compared to HVOF process due to use of air instead of oxygen and high spray rates that reduce spraying time.
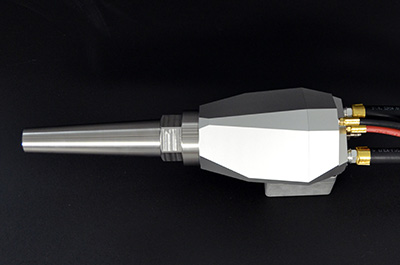
Fuel Types | Air Consumption | Cooling |
Propylene, Propane | 250 SCFM @ 125 PSI | 100% air cooled |
- Highest quality coatings from cemented carbides
- Axial powder injection
- 100% Air Cooling (no water chillers)
- Can spray continously for hours without stopping
- Supports use of Natural Gas
- Low operating cost
- Low consumption of spare parts
- Fast start-up
WC86-Co10-Cr4 |
![]() |